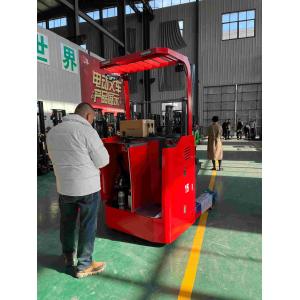
Add to Cart
In modern industrial manufacturing, efficiency and precision remain the dual standards by which equipment is judged. As a key component in smart production lines, the Mandrel Stacker stands out for its superior automation and structural control accuracy. Quietly powering production behind the scenes, it has become an essential tool for improving productivity and product consistency.
A Mandrel Stacker is a piece of equipment used to automatically stack materials—such as metal foils, electrode sheets, or films—onto a mandrel in a neat and accurate manner. Simply put, it precisely, quickly, and reliably "stacks" sheet materials onto a central axis, preparing them for subsequent processes such as winding, hot pressing, or cutting.
Battery Manufacturing: Especially in lithium-ion and solid-state battery production, mandrel stackers are used for stacking electrode sheets before winding or lamination—directly affecting battery performance.
Film Capacitor Production: Where dielectric materials and metal foils need to be stacked precisely to ensure electrical performance.
Precision Metal Processing: Including layered stamping or pre-winding of irregular materials.
Aerospace/Automotive Material Preparation: Pre-stacking of high-performance composite materials.
High-Precision Positioning Systems: Utilizes laser, visual recognition, or servo control to achieve micron-level alignment between materials and mandrel.
High-Speed Automation: Integrated PLC and HMI control systems enable continuous operation with real-time correction, boosting productivity.
Smart and Flexible Handling: Compatible with various material types and sizes, with quick-change capabilities for flexible manufacturing.
Integrated Defect Detection: Real-time monitoring of defects or misalignments enables closed-loop control and reduces waste.
Despite its strong performance, the Mandrel Stacker faces several challenges:
Material Adaptability: Different materials vary in thickness and elasticity, which can affect stacking consistency.
Static Interference: Electrostatic buildup during stacking may cause sheets to stick or misalign.
Thermal and Mechanical Wear: High-speed operation over time may lead to heat deformation or part wear, impacting precision.
To overcome these issues, modern mandrel stackers are increasingly integrating cutting-edge technologies such as:
AI-driven path optimization algorithms
Combined vacuum and electrostatic control systems for better sheet stability
Modular designs for easier maintenance and future upgrades